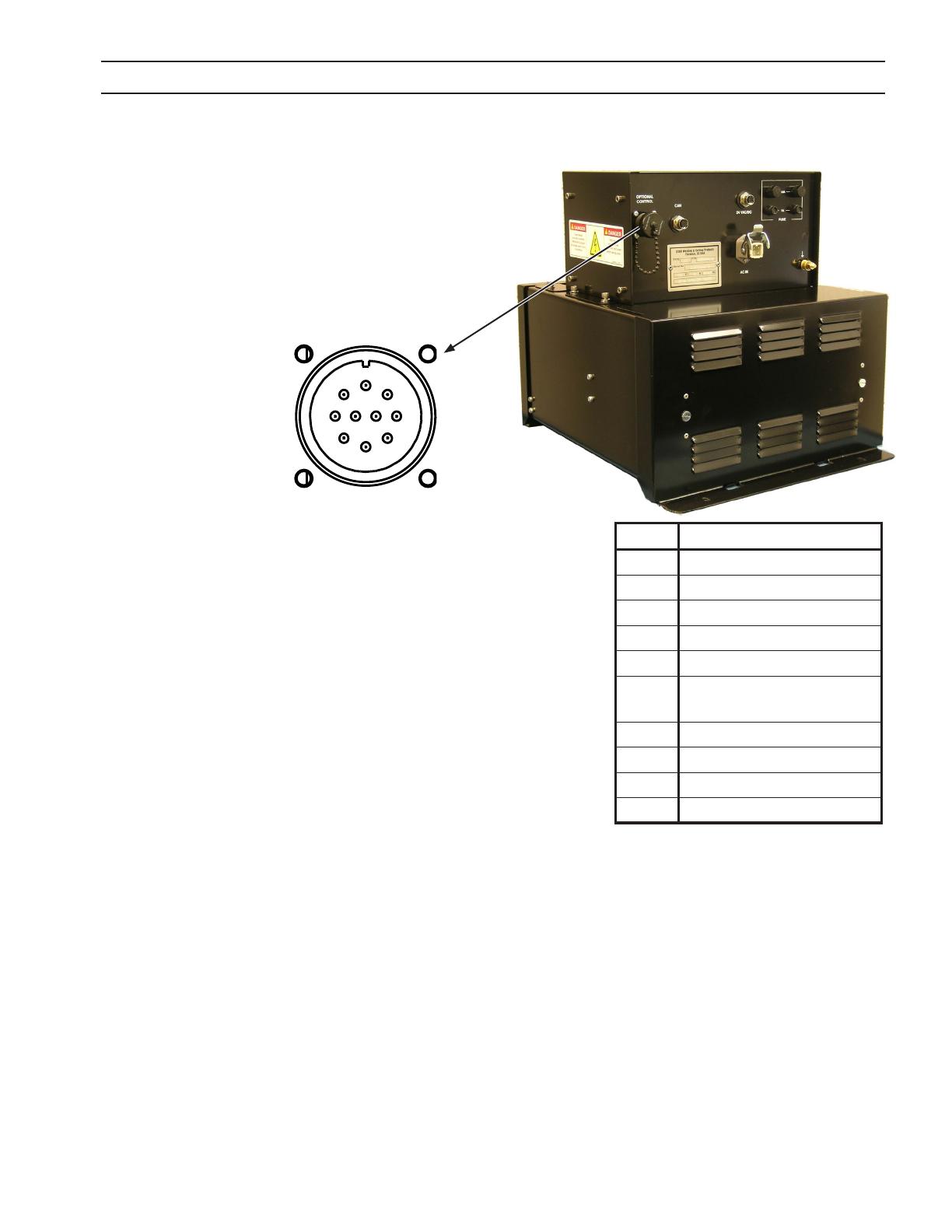
17
SEÇÃO 4 OPERAÇÃO
Quando as comunicações do CAN não estiverem
disponíveis, o WIC poderá funcionar no Modo
de Controle Opcional. Isso acontece quando um
sistema antigo é reformado com a tocha PT-36.
Nesse modo, todos os comandos são enviados
por um conector de 10 pinos com a identicação
“CONTROLE OPCIONAL” no painel traseiro do WIC.
Os sinais desse conector de 10 pinos estão listados
abaixo:
PINO Função
A +24 VDC (SAÍDA)
B Anticongelamento externo
C CNC COM
D Falha
E COM de referência externa
F
Referência de uxo
externo
G Saída de uxo de água
H Saída de pressão de água
J +24 VDC (do Pino A)
K Chassi
O pino A (+24 VDC) é uma saída para o cliente. O cliente precisa enviar
+24 VDC pelo pino B para ativar a função anticongelamento. O pino
D é o sinal de falha, que é normalmente alto, e o pino C é o nível do
sinal. Em caso de falha, o pino D será redenido para baixo. O cliente
precisa monitorar o pino D para vericar se há falhas. O uxo de água é
fornecido pelo sistema via pino E e pino F. Cada volt gera 0,2 gpm, por
exemplo: 5V = >1,0 gpm ou 1V = >0,2 gpm. O sistema também pode
informar o uxo de água e a presão da água para o cliente. Para esses
dois sinais, as relações de mapeamento são: 5V = >1 gpm para uxo, 5V
= >100 psi (6,9 bar) para pressão.
As saídas do pino D (falha), do pino G (saída do uxo de água) e do
pino H (saída de pressão de água) estão disponíveis no Modo de
Comunicação do CAN e no Modo de Controle Opcional.
Para iniciar a bomba, é necessário usar o comando de uxo de água. O uxo mínimo é 0,15 gpm. No Modo de
Controle Opcional, cada volt comandará um uxo de água de 0,2 gpm. No entanto, o comando de uxo deve
atender aos requisitos mínimos. Se um comando de uxo de água do CAN estiver disponível e for maior que o
requisito de uxo mínimo, o WIC ignorará o comando de uxo de água do conector de 10 pinos.
Enquanto a bomba estiver funcionando, o uxo e a pressão da água estarão disponíveis no conector de 10 pinos.
O cliente pode usá-los para solucionar problemas.
4.3 Precaução do motor
A bomba usada nesta aplicação possui um desvio ajustável para manter a pressão em um determinado nível.
Com as congurações de fábrica, a bomba pode aumentar a pressão para um nível 150 psi (10,4 bar) mais alto
que a pressão de entrada. Se for executado continuamente e o uxo for bloqueado, o calor do motor poderá
aumentar a temperatura da água. Isso resultará em um calor excessivo que causará falha no motor.
LAYOUT
DO PINO
DE CONTROLE
OPCIONAL
VISÃO EXTERNA
A
B
C
D
E
F
G
H
J
K
No Modo de Controle Opcional, o Pino A e o Pino J precisam ser
jumpeados para fornecer 24 VDC para o PCUA.
4.2 Operação no Modo de Controle Opcional